Дипломная работа: Шляхи підвищення ефективності роботи малогабаритних кормодробарок
F - зусилля
руйнування зразка матеріалу;
- коефіцієнт корисної дії робочого
органу.
Підставляючи вираз для визначення критичної швидкості
руйнування, і враховуючи, що , одержимо:
;
або:
(3.16)
де S - площа поперечного перерізу
зразка;
F - зусилля
руйнування зразка матеріалу;
Е - модуль пружності
зернівки;
- питома вага зернового матеріалу;
- маса зернівки;
z - кількість
зернівок, що попали під удар одного молотка;
V - об’єм порції
зерна;
Z - кількість
молотків, що подрібнюють;
т - маса молотка;
l c - відстань від осі підвісу до центра мас молотка;
JА - момент інерції молотка.
Дана залежність (3.16) дозволяє визначити корисну
потужність на подрібнення будь-якого виду зернового матеріалу, якщо відомі його
параметри, які характеризують здатність до руйнування, і параметри робочого органу,
причому з урахуванням ступеню зношування молотків.
Розділ 4. Програма та методика
експериментальних досліджень
4.1 Мета і програма експериментальних
досліджень
Метою проведення експериментальних досліджень є
підтвердження або спростування визначених в даній роботі теоретичних положень та
закономірностей відносного руху молотка кормодробарки, впливу показника на технологічний
режим подрібнення та визначення зміни даного показника в процесі зношування молотків
при експлуатації молоткової дробарки.
Для експериментальної перевірки висунутої гіпотези
вибрано методики лабораторних досліджень, вимірювальні пристрої та обладнання. Програма
експериментальних досліджень передбачала:
перевірку достовірності теоретичних залежностей
відносної швидкості молотка від показника лінійних співвідношення ротора співставленням
результатів теоретичних і експериментальних досліджень;
Теоретичні дослідження по обґрунтуванню раціональних
технологічних параметрів подрібнення зернових кормів молотковими дробарками проводилися
з деякими допущеннями. Тому з метою уточнення даних параметрів, для виконання програми
експериментальних досліджень були визначені наступні вихідні положення і напрямки
проведення лабораторних досліджень та виробничих випробувань:
провести математичну обробку експериментальних
даних та встановити інтервал раціональних значень параметрів ротора з шарнірно закріпленими
молотками малогабаритної зернової кормодробарки.
4.2Умови проведення експериментальних
досліджень
Експериментальні дослідження проводилися з метою
уточнення кінематичних параметрів молоткових робочих органів у процесі роботи дробарки,
технологічних параметрів процесу подрібнення зернових кормів, а також з метою перевірки
виконаних нами теоретичних досліджень.
Дослідження проводилися в лабораторії кафедри
"Механізіції тваринництва" Житомирського національного агроекологічного
університету за прийнятими [26] та розробленими методиками на спеціально виготовлених
установках.
Для виконання експерименту використовувалося зерно
пшениці вологістю 12,5 - 14,5 % зі вмістом смітних домішок до 5 % та кількістю пилу
0,26% від загальної маси. Якість вихідного продукту, вологість, та ступінь подрібнення
визначали згідно з ГОСТ 8770 - 58; для вівса - ГОСТ 12770 - 73; для кукурудзи -
ГОСТ 136 - 68; для бобів - ГОСТ 10417 - 74. Проби відбиралися з ГОСТ 13586.3 - 83
“Метод отбора проб”
4.3 Методика проведення досліджень по
вивченню раціональних режимів роботи кормодробарок
З метою виявлення, при
якому з зазначених показників лінійного співвідношення ротора виконується вимога
досягнення максимальної швидкості і мінімальних кутів відхилення молотка в момент
початку удару,
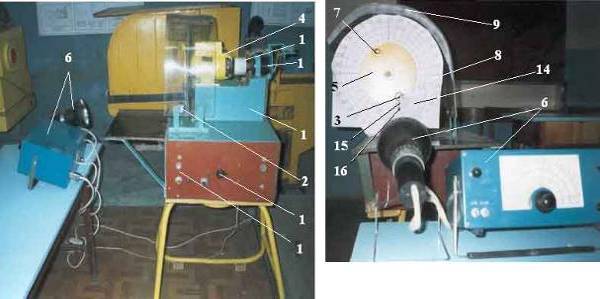
Рис.4.1 Установка для дослідження коливань моделі
молотка:
1 - корпус приладу; 2
- механізм створення опору; 3 - поворотна вісь підвісу; 4 - електродвигун; 5 - диск;
6 - тахометр стробоскопічний 2ТСт 32-456; 7 - противага; 8 - нерухома шкала; 9
- захисний кожух; 10 - регулятор частоти обертання диску; 11 - напівпровідниковий
блок живлення; 12 - механізм вмикання лампи; 13 - тахогенератор; 14 - шкала відхилення
моделі молотка (математичного маятника); 15 - нитка маятника; 16 - стальна кулька
було проведено серію дослідів на спеціально розробленій і виготовленій установці.
На установці (рис.4.1)
маятник, що складається зі сталевої кульки 16 та гнучкої капронової нитки 15, моделює
молоток дробарки, який закріплений на диску з віссю 5 за допомогою гвинта. Таке
закріплення дозволяє легко змінювати довжину маятника і, відповідно, значення показника
лінійного співвідношення між радіусом підвісу ro і зведеною
довжиною молотка lзв.
Вісь підвісу маятника
вільно обертається в підшипниках, що встановлені на диску 5.
У зв'язку з незначністю опорів поворотові осі і
дуже малими масами нитки і кульки маятник установки з достатнім ступенем точності
можна прийняти за математичний, а відстань від осі пальця до центра кульки рівним
приведеній довжині молотка.
Для проведення дослідів
при різних кутових швидкостях диска привід якого здійснюється двигуном 4 постійного
струму (типу ПЛО-7-2 з номінальною потужністю 110 Вт), підключеного через напівпровідниковий
блок живлення 11 до мережі перемінного струму. Регулювання числа обертів виконується
лінійним автотрансформатором 10, включеним у ланцюг обмотки ротора двигуна.
Для виміру швидкості обертання
диска вал двигуна з'єднаний з валом тахогенератора 13, до клем якого підключений
вольтметр, що фіксує частоту обертання диска 5 з маятником. На диску закріплена
шкала кутових амплітуд коливань маятника 14, що обертається разом з диском 5. Центр
цієї шкали сполучений з віссю підвісу маятника, а її нульова відмітка розташована
на радіусі диска, що проходить через вісь підвісу.
Положення шкали 14 і разом
з нею осі підвісу маятника в кожен момент часу можна визначати по круговій шкалі
8, закріпленій разом із захисним кожухом 9 нерухомо на корпусі 1. Нульова відмітка
нерухомої шкали розташована внизу. При кожному обороті вала контакт механізму вмикання
12, установлений на рухомому текстолітовому кільці, замикає сталеві пружинні контакти
електричного ланцюга стробоскопа 6. Безінерційна лампа стробоскопа при кожному обороті
висвітлює на мить диск, маятник і тоді його шкала представляються спостерігачеві
нерухомими.
Це дозволяє відраховувати
по нерухомій шкалі 8 кут повороту осі, а по рухомій шкалі 14 - кут відхилення маятника
від радіально - рівноважного положення. Механізм вмикання лампи 12 дозволяє вільний
поворот втулки на будь - який кут. Обмежується поворот втулки кутом у 360º
за допомогою гвинта і пружного, нерухомо закріпленого обмежувача.
Поворотом втулки разом
із пружинними контактами, здійснюваним при обертанні диска, досягається зміна моменту
включення лампи стробоскопа і, відповідно, миттєве висвітлення маятника при будь-яких,
наперед обраних положеннях його осі підвісу.
Коливання маятника збуджуються
механізмом створення опору 2 (рис.4.4), що складається з гумової пластини, об яку
при кожному оберті диска вдаряється кулька маятника. Пластина з допомогою кронштейна
закріплена на гвинті, підйом і опускання якого здійснюється поворотом гайки (рис.4.2,
поз.6).
Поворотові гвинта при
цьому перешкоджає шпонка, установлена на корпусі приладу що вільно входить в подовжній
паз гвинта. Регулюванням розташування пластини по висоті досягається удари кульки
по однієї і тій же площадці пластини при різній довжині маятника. Ця площадка відзначена
пофарбованою плямою.
Реакція пластини імітує
реакцію порцій матеріалу, що подрібнюється, які надходить у дробильну камеру.
При русі в продуктово-повітряному
шарі робочої камери відбувається безліч зіткнень молотка з твердими частками шару,
але вони менш інтенсивні, мають безладний, хаотичний, неперіодичний характер. Зіткнення
ж молотків з порціями матеріалу, що надходять у камеру, мають періодичний характер,
що визначає коливання молотка. Тому дослідження періодичних коливань маятника проведені
з одною пластиною.
Експеримент проводився
в наступній послідовності.
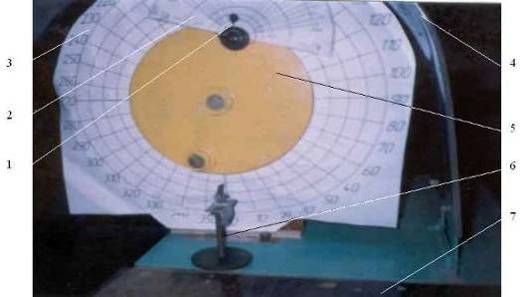
Рис.4.2 Дослідження руху моделі молотка кL= 4:
1 - модель молотка (математичний маятник), 2 -
шкала кутового відхилення моделі молотка, 3 - шкала кутового положення осі підвісу
моделі молотка, 4 - захисний кожух, 5 - диск, що обертається, 6 - механізм створення
опору, 7 - опорний стіл
Відстань rо
від осі обертання диска до осі підвісу маятника у всіх дослідах цієї серії постійна
і дорівнює 0,09 м. Довжина lзв маятника послідовно встановлювалась
рівною 0,0225; 0,030; 0,040; 0,060 м, що відповідало значенням показника лінійного
співвідношення kL 4; 3; 2,25; 1,5. З метою збереження
постійної величини кінетичної енергії кульки при удару на різних довжинах маятника
кутові швидкості обертання wе диска підбиралися так, щоб величина кінетичної енергії
була постійною.
Для маятника довжиною
lзв= 0,030 м
прийняте wе30=104,7 с-1 (відповідне n=1000 об/хв), відповідно прийняті
wе22,5=111,7 с-1, wе40=96,6 с-1, wе60=83,8 с-1, wе90=69,8 с-1.
З маятником довжиною
lзв=0,040 м (kL=2,25) досліди проведені
також при кутових швидкостях обертання we=733; 104,7; 125,6; 175,1 с-1. При прийнятих значеннях we30 відцентрова сила маси кульки маятника більше сили ваги
в:
раз,
у зв'язку з чим коливання,
викликані змінами моменту гравітаційних сил ваги маятника при його обертанні, настільки
незначні, що в дослідах, проведених без удару кульки об пластину (пластина опущена),
відхилення маятника від радіально-рівноважного стану в усіх положеннях осі підвісу
не були помічені [52].
4.4 Методика визначення енергетичних показників
роботи молоткової кормодробарки
Для визначення витрат
енергії на подрібнення зернових кормів було вдосконалено стенд для дослідження процесу
роботи молоткової кормодробарки (рис.4.1 і рис.4.2), що дає можливість визначити
раціональні параметри фізичного маятника по куту відхилення при взаємодії з шаром
зернових кормів і при цьому фіксувати витрачену потужність [52].
Виконання фізичного маятника
у вигляді сталевого пластинчатого молотка виключає похибку від еластичності нитки
фізичного маятника, що наближує умови проведення експерименту до відповідного процесу
у молотковій кормодробарці. Вдосконалення джерела живлення забезпечує можливість
визначати потужність, затрачену в процесі роботи, а встановлення прозорої передньої
стінки захисного кожуха дає змогу контролювати фізичні параметри процесу подрібнення
зернових матеріалів.
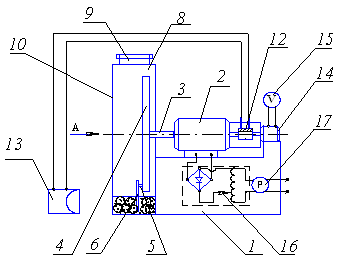
Вид А
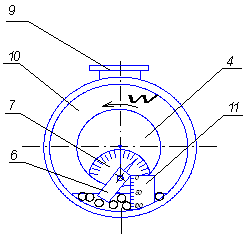
Рис.4.3 Схема стенду
для дослідження роботи молоткової дробарки:
1 - корпус, 2 - електродвигун, 3 - вал, 4 - диск,
5 - вісь маятника, 6 - молоток, 7 - шкала кутових відхилень, 8 - кожух, 9 - горловина,
10 - передня стінка, 11 - шкала товщини шару, 12 - механізм замикання контактів.13
- стробоскоп, 14 - тахогенератор, 15 - вольтметр, 16 - джерело живлення, 17 - прилад
К - 505
Стенд для дослідження
процесу роботи молоткової дробарки (рис.4.3) містить корпус 1, де встановлено електродвигун
постійного струму 2, на одному кінці вала 3 якого закріплено диск 4 з віссю 5, на
якій навішений фізичний маятник у вигляді пластинчатого молотка 6. На диску 4 розміщена
шкала 7 для визначення кутових відхилень молотка 6. Зона обертання диска 4 захищена
циліндричним кожухом 8 з горловиною 9 для завантаження кормів у верхній частині
та прозорою передньою стінкою 10, на якій є шкала 11 для визначення товщини шару
зернових кормів. На вільному кінці вала 3 встановлено механізм замикання контактів
12 стробоскопічної лампи 13 і тахогенератор 14, пов’язаний з вольтметром 15 для
визначення частоти обертання вала двигуна 2, що живиться від джерела постійного
струму 16.
Джерело живлення дає можливість
змінювати напругу (частоту обертання ротора) та приладом 17 вимірювати потужність,
затрачену на подрібнення при значенні показника лінійного співвідношення кL=2,25
та кL=4.
На вісь 5 шарнірно кріпиться
фізичний маятник у вигляді пластинчатого молотка 6. Подаючи напругу від джерела
живлення 16 на електродвигун 2, встановлюємо частоту обертання диска 4 згідно програми
експерименту, і контролюємо швидкість обертання вольтметром 15, ввімкненим у ланцюг
тахогенератора 14. Відхилення молотка 6 при взаємодії з шаром зернових кормів, що
завантажені у циліндричний кожух 8 з прозорою стінкою 10 визначаємо по шкалі 7 при
вмиканні стробоскопу 13.
Положення точки зняття
показань відносно місця контакту “молоток - матеріал” вибирається поворотом механізму
вмикання 12 відносно осі обертання вала 3 електродвигуна 2.
Затрачену в процесі роботи
стенду потужність при різних технологічних режимах вимірюємо приладом 17. Встановлення
прозорої передньої стінки 10 дає можливість візуального спостереження за динамікою
руху фізичного маятника у вигляді пластинчатого молотка 6 зі зняттям показань його
кутових відхилень при взаємодії з шаром зернових кормів при обертанні диска 4. Використання
приладу 17 дає можливість визначити потужність при роботі стенда на різних технологічних
режимах.
4.5 Методика визначення якості подрібнення
зернового матеріалу. Критерій оцінки ефективності роботи молоткових дробарок
Якість подрібнення зерна визначалася по ГОСТ 134986.8
- 72 “Комбикорма. Методы определения крупности размола и содержания неразмолотых
семян культурных и дикорастущих растений” [10]. При цьому у пробі масою 100 г допустимі норми втрат не повинна перевищувати 1 %, розбіжність в одному й тому ж зразку ±0,1 % а
між контрольним і арбітражними аналізами ± 0,2 %.
Згідно ДСТУ 2421-94“Комбiкорми. Термiни та визначення”
[16] та ДСТУ 4508: 2005 “Комбікорми-концентрати для свиней. Технічні умови"
[17] залишок на ситі діаметром 3 мм не повинен перевищувати 5 - 12 % для різних
вікових та статевих категорій свиней та 10 - 30 % для ВРХ. Залишок на ситі діаметром
5 мм допускається тільки для беконної та м’ясної відгодівлі свиней у межах не більш
одного проценту, та відгодівлі дорослої ВРХ, дійних корів і биків - виробників не
більше 5 %
Для того щоб оцінити якість роботи дробарки та
порівняти ефективність подрібнення при різних коефіцієнтах лінійних співвідношень,
був використаний ситовий класифікатор кулісного типу.
Класифікатор для проведення гранулометричного аналізу
зернової суміші (рис.4.4) складається з мотор-редуктора (електродвигун постійного
струму типу 2ПП-40 потужністю Ne=70Вт, нормальною
частотою обертання валу ne=4100об/хв та черв’ячний редуктор
з передавальним числом U=51); насадженого на його вал кривошипа з
пальцем; куліси, у прорізі якої знаходиться палець кривошипу; паралелограмного механізму,
ведучою ланкою якого є продовження куліси, вертикальною ланкою, що поступально рухається
- набір лабораторних сит, механізму кріплення сит, горизонтальною веденою ланкою
- коромисло, нерухомою ланкою - стійка. Ланки паралелограмного механізму між собою
шарнірно з’єднані пальцями. Конструкція механізму кріплення дозволяє легко та швидко
знімати набір сит, змінювати кількість сит у ньому.
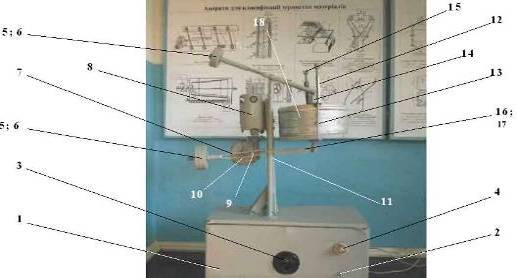
Рис.4.4 Ситовий кулісний класифікатор для гранулометричного
аналізу зернового матеріалу після подрібнення: 1 - підставка; 2 - тумблер, 3 - регулятор автотрансформатора;
4 - лампа сигнальна; 5 - противага; 6 - гайка; 7 - куліса; 8 - електродвигун; 9
- палець кривошипа; 10 - кривошип; 11 - стійка; 12 - втулка; 13 - стрижень; 14
- поперечка; 15 - гайка-баранчик; 16 - палець; 17 - коромисло; 18 - ситовий набір
Стійка закріплена на кришці основи класифікатора.
В середині основи розташований лінійний автотрансформатор. Обертанням рукоятки змінюється
напруга в роторі електродвигуна, чим досягається встановлення потрібної частоти
обертання двигуна. Двигун приєднаний до мережі перемінного струму напругою 220
В, через трансформатор з напругою на вторинній обмотці 24 В
та випрямляючим містком. Для вмикання електродвигуна є тумблер, а для сигналізування
про його роботу - неонова лампочка. З метою зміни амплітуди коливання сит кривошип
під кріплення пальця кривошипу декілька отворів, які дають можливість встановлювати
радіус кривошипу 0,020; 0,030; 0,040; 0,050 м. Врівноваження набору сит відбувається противагою, закріпленою на кінцях куліси та коромисла. При вмиканні електродвигуна
кривошип, який обертається з його валом, передає кулісі та з’єднаним з нею набором
сит інтенсивне коливання. Ситовий аналіз проводиться для визначення ефективності
та основних параметрів процесу подрібнення зерна виконується в наступній послідовності:
1.
Відбираємо з кожного пакета пробу в поліетиленові стаканчики.
Вага кожної проби повинний складати 0,100 кг. Зважування проби робимо на лабораторних вагах типу ВЛКТ-500г.
2.
Вибираємо для класифікатора комплект сит: 1-е сито
- ø1 мм, 2-е сито - ø2 мм і 3-е сито - ø3 мм.
3.
Установлюємо на класифікатор ситовий піддон, три сита
і кришку сит, весь набір фіксується.
4.
Регулюємо режим роботи класифікатора: амплітуда коливань
- 0,1 м, частота коливань 110.120 хв-1.
5.
На верхнє решето класифікатора висипаємо приготовану
пробу подрібненої зернової суміші, закриваємо кришкою, закріплюємо набір решіт на
платформі класифікатора.
6.
Включаємо електродвигун і протягом 3 хвилин робимо сортування
здрібненої зернової суміші на фракції.
7.
Кожну фракцію, що залишилася на решетах, а також
"прохід" нижнього решета зважуємо на лабораторних аналітичних вагах типу
ВЛКТ-500г.
8.
Отримані результати гранулометричного складу фракцій
заносимо в таблицю.
9.
Розраховуємо масу кожної фракції в процентному вмісті
В (%) цієї фракції стосовно вихідного навішення по "сходу" і "проходу".
Середній розмір часточок dі ср визначається
як середнє арифметичне діаметрів верхнього і нижнього сита:
Страницы: 1, 2, 3, 4, 5, 6, 7, 8, 9
|