Курсовая работа: Очистка газов, основанная на катализе
2. Активный металлический катализатор на носителе из оксида металла.
Например, тонкий слой металла платиновой группы наносят на носитель - обожженный
α-оксид алюминия либо фосфор (свечного типа). Носитель изготавливают в виде
цилиндрических гранул, расположенных рядами, смещенными по отношению друг к другу.
Катализатором может быть также γ-оксид алюминия с большой
удельной поверхностью и платиновым покрытием. К этой же группе относится палладиевый
катализатор на носителе из оксида алюминия.
3. Активный катализатор - оксид металла на подложке из оксида
металла. Активные оксиды (например, γ-А12О3), обладающие
высокой удельной поверхностью, могут быть нанесены на носитель из оксида металла
(например, на γ-А12О3). Такая система обладает следующими
преимуществами: она способна выдержать высокие температуры; в ее состав входят дешевые
материалы (по сравнению с катализаторами из благородных металлов); кроме того, она
может быть изготовлена в виде стержней или таблеток.
К этой категории относят также катализаторы, целиком состоящие
из активного материала, включая и носитель; такие катализаторы называют иногда
"бесподложечные". К их числу относят смесь оксидов меди и марганца
("Хопкалит"), обеспечивающую полное сгорание углеводородов при 300-400°С,
за исключением метана (30% при 400°С).
4. Активный оксид металла на металлическом носителе. Например,
каталитическая система, представляющая собой металлическую проволоку в качестве
носителя. В процессах очистки газов такие системы практически не используются.
В настоящее время разрабатываются комплексные катализаторы, обладающие
активностью к нескольким реакциям (при обезвреживании нескольких вредных веществ).
Температура, которая обычно необходима для начала каталитической
реакции (температура зажигания), зависит от присутствующих в газе веществ и типа
катализатора. Для некоторых веществ температура зажигания приведена в табл.1.
Таблица 1 - Температура
зажигания катализаторов при каталитическом окислении.
Загрязняющее вещество в очищаемых газах |
Температура каталитического окисления,°С |
Альдегиды, антрацены, пары масла, углеводороды |
320-370 |
Водород, оксид углерода, метан, углерод |
650-980 |
Оксид углерода, углеводороды |
340-450 |
Парафины, пары масел |
320-370 |
Водород, метан, оксид углерода, формальдегид |
340 |
Растворители, смолы |
260-400 |
Фенол |
320-430 |
Маленовая и фталевая кислоты, нафтахиноны, оксид углерода, формальдегид |
320-340 |
Углеводороды |
260-650 |
Растворители |
320 |
Углеводороды |
320-370 |
Растворители, лаки |
320-370 |
Важнейшим требованием к катализаторам, используемым в очистке
газов, является стойкость к каталитическим ядам.
Рассмотрим действие основных каталитических ядов на катализаторы
при очистке выбросов.
Фосфорорганические соединения, встречающиеся в аэрозолях, образуемых
смазками, при окислении дают фосфорную кислоту, которая покрывает катализатор тонким
дезактивирующим слоем.
Тяжелые металлы - свинец и мышьяк - действуют подобно фосфатам,
образуя тонкие дезактивирующие пленки. Дезактивация и засорение катализатора могут
быть обусловлены присутствием пыли в очищенном газе.
Если эта пыль огнеупорная (оксиды алюминия, кремния и железа),
ее дезактивирующее действие может быть постоянным; если не произошло спекание, фильтрующие
элементы могут быть очищены и активность катализатора частично восстановится.
Временная потеря активности может быть вызвана отложением мелкой
угольной пыли и сажи вследствие неполного сгорания. В этом случае уголь выжигается
из катализатора при кратковременном повышении температуры до 350°С.
Стоимость катализатора зависит от стоимости исходного сырья и
технологии его получения. Часто для приготовления катализаторов используют драгоценные
и редкие металлы: платину, серебро, радий, палладий, рутений, церий и другие, а
также цветные металлы: медь, цинк, хром, никель кобальт, олово, алюминий, титан,
молибден и другие. С целью снижения стоимости следует синтезировать, где это возможно,
катализаторы, не содержащие драгоценных металлов или снижать их содержание. В ряде
случаев такие катализаторы по активности и другим показателям не уступают катализаторам,
в состав которых входят драгоценные металлы.
Немаловажное влияние на стоимость катализаторов оказывает технология
их приготовления. Технология получения катализаторов зависит от того, в каком виде
его получают. Например, в виде металлических сеток, гофрированной ленты, керамических
блоков, таблеток, колец, шариков и др. Наиболее часто контактные массы получают
в виде таблеток путем совместного осаждения каталитически активных веществ с последующим
добавлением активаторов и наполнителей.
Производство таких катализаторов включает следующие стадии: подготовку
сырья, растворение, осаждение, фильтрование, промывку, сушку, прокаливание, формовку.
1.4 Конструкция каталитических реакторов
Требования к конструкции:
–
высокая производительность;
–
обеспечение непрерывности процесса при оптимальных технологических режимах;
–
легкость в управлении;
–
возможность автоматизации;
–
малое гидравлическое сопротивление;
–
доступность загрузки и выгрузки катализатора;
–
наличие устройства для подогрева газовых смесей и рекуперации тепла;
–
небольшая металлоемкость, доступность монтажа, ремонта и транспортировки.
По способу взаимодействия газов с катализатором аппараты подразделяются
на 3 группы:
1. Каталитические реакторы с фильтрующим слоем катализатора.
К аппаратам с фильтрующим слоем относятся емкостные, трубчатые и полочные аппараты,
принцип действия которых основан на фильтрации газа через слой неподвижного катализатора
(рис.1). На этом принципе основана работа большинства контактных аппаратов.
Причем катализатор может находиться в виде металлических сеток,
натянутых по ходу движения газа, трубчатых контактных аппаратов или в виде твердых
тел различной формы, располагаемых на перфорированных решетках. Достоинства таких
аппаратов: простота конструкции. К недостаткам следует отнести отсутствие теплообмена,
что позволяет проводить в них только те реакции, которые сопровождаются небольшими
тепловыми эффектами.
Для полноты протекания процесса в одном аппарате может быть установлено
несколько слоев контактной массы.
Многослойные контактные аппараты чаще всего устанавливают, когда
имеется необходимость очищаемый газ подвергать дополнительной обработке (нагреванию,
охлаждению и т.д.). Это позволяет вести процесс при оптимальном температурном режиме
на каждой полке.
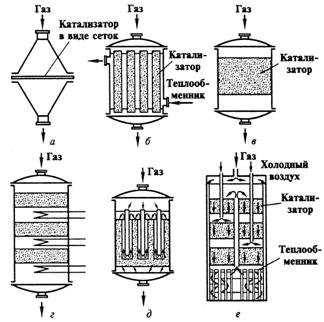
Рис.1. Схемы контактных аппаратов с фильтрующим слоем катализатора:
а - контактный аппарат с катализатором в виде сеток; б
- трубчатый контактный аппарат; в - контактный аппарат с перфорированными
решетками; г - многослойный контактный аппарат; д - контактный аппарат
с трубками Фильда; е - контактный аппарат с теплообменником
В зависимости от функционального назначения контактные аппараты
с фильтрующим слоем катализатора имеют несколько вариантов конструктивного оформления:
реакторы каталитические с твердым катализатором, размещенном в отдельном корпусе
(тип К); реакторы каталитические, в которых в общем корпусе размещены контактный
узел и подогреватель (тип ТК); реакторы термокаталитические, в которых в общем корпусе
размещены контактный узел и рекуператор тепла (тип KB);
реакторы каталитические, в которых в общем корпусе размещены подогреватель, контактный
узел и рекуператор тепла (тип ТКВ). Наиболее перспективными являются аппараты ТКВ,
которые в максимальной степени отвечают экологическим требованиям.
Например, термокаталитический дожигатель конструкции Гипрогазочистка
(рис.2).
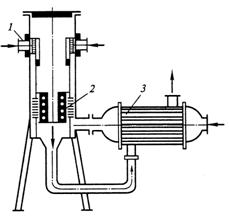
Рис.2. Каталитический дожигатель конструкции Гипрогазочистка:
1-горелка; 2-слой катализатора;
3-теплообменник-рекуператор.
Газ, содержащий вредные примеси, подогревается очищенными газами
в теплообменнике-рекуператоре. Затем смешивается с топочными газами, образующимися
при сжигании топлива в горелках 1, после чего происходит обезвреживание на
поверхности катализатора 2.
Недостатком аппаратов с фильтрующим слоем является возможность
засорения катализатора твердыми частицами. В этом случае могут быть использованы
трубчатые реакторы с нанесенными на внутреннюю поверхность трубок катализаторами.
Для отвода (подвода) тепла из реакторов с неподвижным слоем используют
теплообменники, расположенные вне слоев катализатора.
2. Каталитические реакторы со взвешенным слоем катализатора.
Недостатком фильтрующего слоя является наличие зон, плохо омываемых газом в
местах соприкосновения гранул катализатора. Для устранения этих недостатков используют
кипящий слой, в котором каждая гранула катализатора интенсивно (рис.3), со всех
сторон соприкасается с газом, что интенсифицирует процесс очистки.
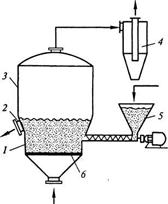
Рис.3. Каталитический реактор с кипящим слоем катализатора:
1 - цилиндрическая часть корпуса;
2 - зернистый катализатор; 3 - верхняя часть корпуса; 4 - циклон; 5 - шнековое
устройство; 6 - газораспределительная решетка.
Достоинством таких аппаратов является также хорошая теплопроводность
слоя, возможность механизировать и интенсифицировать процесс загрузки и выгрузки
катализатора, исключение возможности локального перегрева или переохлаждения, возможность
использовать мелкий катализатор (в фильтрующем слое мелкозернистый катализатор не
используется из-за повышенного сопротивления и неравномерности температурного слоя).
К недостаткам взвешенного слоя следует отнести истирание и унос
пылевидного катализатора из аппарата, что требует установки пылеулавливающего аппарата
и предъявляет повышенные требования к прочности катализаторов, а также невозможность
осуществления противотока, что снижает движущую силу процесса. Перечисленные недостатки
не являются определяющими и многие из них могут быть полностью или частично устранены.
Для упорядоченного перемешивания твердой фазы в кипящем слое
иногда вводят механические мешалки, что способствует усреднению времени пребывания
частиц в аппарате.
Для увеличения степени очистки газов используют многополочные
аппараты с кипящем слоем.
Для отвода (подвода) тепла из реакторов со взвешенным слоем используют
теплообменники, расположенные внутри слоев катализатора.
3. Каталитические реакторы с пылевидным катализатором. В
аппаратах с пылевидным катализатором измельченный катализатор распыляют в рабочую
зону с помощью специальных сопел (рис.4). Этим достигается более полное использование
реакционного объема. Реакция протекает в тот момент, когда частицы катализатора
находятся в полете.
Обычно процессы каталитического восстановления и окисления рассматривают
отдельно.
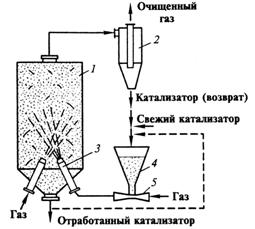
Рис.4. Каталитический реактор с пылевидным реактором:
1 - цилиндрический корпус; 2 - циклон; 3 - сопло; 4
- бункер; 5 - эжекторное устройство
Каталитическое окисление используют для удаления диоксида серы
из дымовых газов, очистки выбросов от окиси углерода, органических веществ, а каталитическое
восстановление для обезвреживания газов от оксидов азота.
После каталитического окисления газы направляют на дальнейшую
переработку, например, абсорбцию, с получением готового продукта. Для некоторых
газов эта стадия не предусмотрена, так как загрязнитель превращается в безвредное
соединение.
2. Технологическая часть
2.1 Технологическая схема и ее описание
Типичной является схема установки каталитического обезвреживания
отходящих газов в производстве клеенки, показанная на рис.5. В газовых выбросах
этих производств, поступающих из камер сушки клеенки, присутствует пары керосина
(100-1000 мг/м3), уайт-спирита (до 200 мг/м3) и ряда органических
соединений.
Отходящие из сушильного агрегата газы при 80-200°С вентилятором
через брызгоотбойник подают в теплообменник для предварительного подогрева теплом
конвертированных газов до 200-220°С, а затем в подогреватель, где их температуру
увеличивают до 250-327°С за счет тепла дымовых газов, получаемых сжиганием газообразного
топлива. Для сжигания используют кислород, содержащийся в очищаемых газах. Сжигание
органических примесей до СО2 и Н2О проводят в реакторе на
катализаторе. Конвертированные газы из реактора через теплообменник вентилятором
возвращают в сушильный агрегат. С целью компенсации потерь кислорода и доведения
температуры обезвреженных газов до уровня, соответствующего условиям сушки клеенки
(120-170°С), перед поступлением в сушильный агрегат их разбавляют воздухом. Часть
прошедших очистку газов сбрасывают в атмосферу. При использовании алюмоплатинового
катализатора полная очистка при объемной скорости 40 тыс. ч‾1 достигается
при 290°С, более высокая температура (350°С) необходима для обеспечения того же
эффекта при объемной скорости газа 60 тыс. ч‾1.
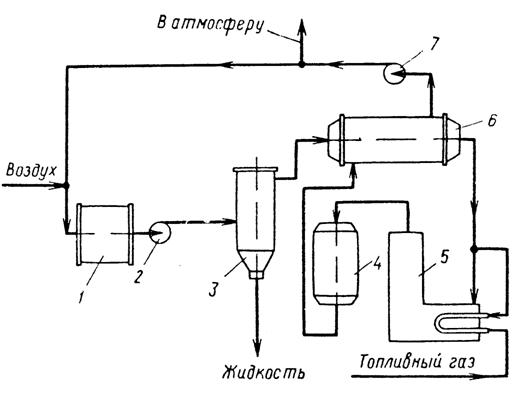
Рис.5. Схема установки каталитического дожигания отходящих газов:
1 - сушильная камера; 2, 7 - вентиляторы; 3 - брызгоотбойник;
4 - теплообменник; 5 - подогреватель; 6 - реактор
3. Расчетная часть
Определяем основные размеры реактора для каталитического окисления
вредных примесей промышленного выброса.
Исходные данные: объем выброса G’= 12000
м3/ч; температура выброса 15°С;
температура в реакторе 250°С; ПДК фенола 0,01 мг/м3; катализатор - АП-56 имеет следующую характеристику:
диаметр частиц 0,003 м, длина частиц 0,005 м, форма - цилиндрическая, порозность слоя катализатора e = 0,375; требуемая степень очистки по веществу с меньшей
ПДК, т.е. по фенолу 0,997.
Химический состав выброса, % (об.): азот - 78, кислород - 21,
пары воды - 0,5, диокид углерода - 0,5.
Концентрация вредных примесей, г/м3: фенол - 1,45.
Расчет.
Кинетическое уравнение окисления фенола на катализаторе АП-56:
Фенол - АП - 56 |
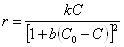
|
k0=1,06*107;
Е=55268 кДж/моль;
b0=1, 19*10-7;
Q=67829 кДж/моль
|
где r - скорость химической реакции,
г/ (м3*с);
k - константа скорости химической
реакции, с-1;
C - концентрация окисляемого вещества,
г/м3;
b - коэффициент кинетического уравнения;
k0, b0 - предэкспоненциальные множители
E - энергия активации, кДж/моль;
Q - энергия адсорбционных стадий,
кДж/моль;
R - универсальная газовая постоянная,
кДж/ (моль*К);
T - температура, К;
m, x
- показатели степени в кинетических уравнениях.
1. Конечная концентрация фенола:
СК = 1,45 (1 - 0,997) =0,00435 г/м3.
2. Необходимое число единиц переноса

где Сн, Ск, - начальная и конечная концентрация
окисляемого вещества, г/м3.
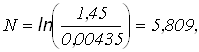
3. Скорость фильтрования принимаем uф
= 0,5 м/с.
4. Коэффициент массопередачи определяют по формулам
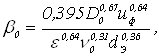
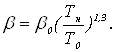
где D0 - коэффициент диффузии, м2/с;
ε - порозность слоя катализатора, м3/м3;
ν0 - кинематическия вязкость воздуха при нормальной
температуре, м2/с;
dэ - эквивалентный диаметр
каналов слоя катализатора, м.
Для этого рассчитаем некоторые величины.
4.1 Коэффициент диффузии вычисляем из выражения

где VА, VВ - мольные объемы окисляемого
вещества и воздуха соответственно;
МА, МВ - молекулярные массы окисляемого
вещества и воздуха;
Р0 - атмосферное давление, МПа.
Мольный объем фенола С6H6O VA = 16,5 6 + 1,98 6 + 5,48 - 20 = 96,36, мольный объем воздуха
VB = 20,1, молекулярная
масса фенола МА = 94,12, молекулярная масса воздуха МВ = 29,
давление Р0 = 0,1 МПа.
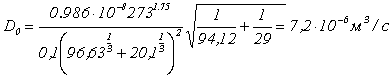
4.2 Удельная поверхность слоя цилиндрических частиц
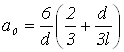
где d, l - диаметр и длина частицы соответственно, м.

4.3 Эквивалентный диаметр каналов, образованных частицами катализатора:
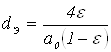

4.4 Конечная температура катализатора Тк рассчитывается
по формуле:
Тк=Тн+gа. р (Сн-Ск),
где qа. р. - удельная
величина адиабатического разогрева, м3 К/г.
Величину qа. р вычисляют по
формуле
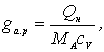
где QH - теплота
сгорания окисляемого вещества, кДж/моль;
cV - теплоемкость
воздуха, кДж/ (м3 К), равная

где ср - теплоемкость воздуха при постоянном давлении,
кДж/ (моль К), ср = 30 кДж/ (моль × К).
Теплоту сгорания органического вещества находят из соотношения
Qн=393,6·nC+121,0·mH
где nC, mH - число атомов углерода и водорода в молекуле вещества.
Qн=393,6·6+121,0·6=3087,6
кДж/моль,


Тк=523+33,96· (1,45-0,0084) =572,09 К
4.5 Средняя температура катализатора:
Тс = 0,5· (Тн + Тк) = 0,5·
(523+572,09) =547,58 К

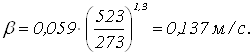
5. Удельная доступная поверхность катализатора:
а=а0 (1-ε) φ,
где а0 - удельная поверхность слоя катализатора,
м2/м3;
φ - коэффициент доступной поверхности, φ=0,85.
а=1733· (1-0,375) ·0,85=920,66 м2/м3.
6. Высота слоя по массопередаче:
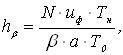
где N - необходимое число единиц
переноса;
β - коэффициент массопередачи, м/с;
а - удельная доступная поверхность катализатора, м2/м3;
uф - скорость фильтрования,
м/с;
Тн - температура в реакторе, К; Т0 =273
К.

7. Константа скорости реакции окисления фенола:
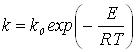

8. Коэффициент кинетического уравнения:
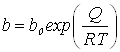

9. Скорость реакции окисления фенола:
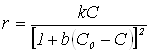

10. Составляющая высота слоя по кинетике рассчитывается по формуле:
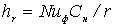

11. Рабочая высота слоя катализатора:
h= (1.25÷1.45) hр = 1,35·0,06208=0,083808 м
hр=hβ+hr = 0,0441+0,01798=0,06208 м
12. Необходимая поверхность фильтрования:
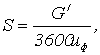
где G' - объем промышленного выброса, м3/ч.
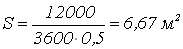
13. Объем катализатора составит Vк (м3):

где Н - рабочая высота кольцевой корзины, м; Dср - средний диаметр кольца, м. Принимаем кольцевую
корзину, у которой отношение H/Dср
= 2, тогда Н=2·1,03=2,06 м

Выводы
В курсовой работе проведен анализ и изучен каталитический метод
очистки отходящих газов. Этот метод очистки основаны на химических превращениях
токсичных компонентов в нетоксичные на поверхности твердых катализаторов. Очистке
подвергаются газы, не содержащие пыли и катализаторных ядов. Методы используется
для очистки газов от оксидов азота, серы, углерода и от органических примесей.
Так же рассмотрены катализаторы, применяемые для этого метода.
Катализаторы для таких процессов приготовляют на основе меди, хрома, кобальта, марганца,
никеля, платины, палладия и других металлов. В отдельных случаях используют некоторые
природные материалы (бокситы, цеолиты).
Изучены конструкции различных каталитических реакторов. Рассмотрена
и представлена схема установки каталитического обезвреживания.
Произведен расчет каталитического реактора с катализатором -
АП-56. Вычислены его основные размеры: диаметр, высота и объем.
Используемые в промышленной практике установки каталитической
очистки газовых выбросов от паров органических веществ различаются конструкцией
контактных аппаратов, способами повышения до необходимого уровня температуры поступающих
в них газовых потоков, используемыми катализаторами, приемами рекуперации тепла,
наличием рецикла обезвреженных газов.
Список использованной литературы
1.
Родионов А.И., Клушин В.Н., Торочешников Н.С. / Техника защиты окружающей
среды / - М.: Химия, 1989. - 511 с.
2.
Родионов А.И., Клушин В.Н., Систер В.Г. /Технологические аспекты экологической
безопасности - Калуга: изд.Н. Бочкаревой, 200. - 800 с.
3.
Юшин В.В., Попов В.М., Кукин П.П. и др. /Техника и технология защиты воздушной
среды - М.: Высш. шк., 2005. - 391 с.
4.
Защита атмосферы от промышленных загрязнений / Справ. изд. в 2-х ч. под ред.
Калверта С., Инглунда Г. / - М.: Металлургия, 1988. - 758 с.
5.
Страус В. /Промышленная очистка газов/ пер. с англ. - М.: Химия, 1981. -
616 с.
6.
Кузнецов И.Е., Троицкая Т.М. /Защита воздушного бассейна от загрязнений предприятиями
химической промышленности / - М.: Химия, 1974. - 474 с.
7.
Павлов К.Ф., Романков Н.Г., Носков А.А. Примеры и задачи по курсу процессов
и аппаратов химической технологии. Л.: Химия, 1981, 560 с.
8.
Иоффе И.Л. Проектирование процессов и аппаратов химической технологии. Учебник
для техникумов. - Л.: Химия, 1991 г. - 352с.
9.
Дытнерский Ю.И. Основные процессы и аппараты химической технологии: Пособие
по проектированию. - М.: Химия, 1991 г. - 496с.
10.
Плановский А.Н., Рамм В.М., Каган С.З. Процессы и аппараты химической технологии.
Учебник для техникумов. - М.: Химия, 848 с.
11.
Дытнерский Ю.И. Процессы и аппараты химической технологии: Учебник для вузов.
Изд.3-е. В 2-х кН. М.: Химия, 2002 г.
|